COORDINATE MEASURING MACHINES (CMM)
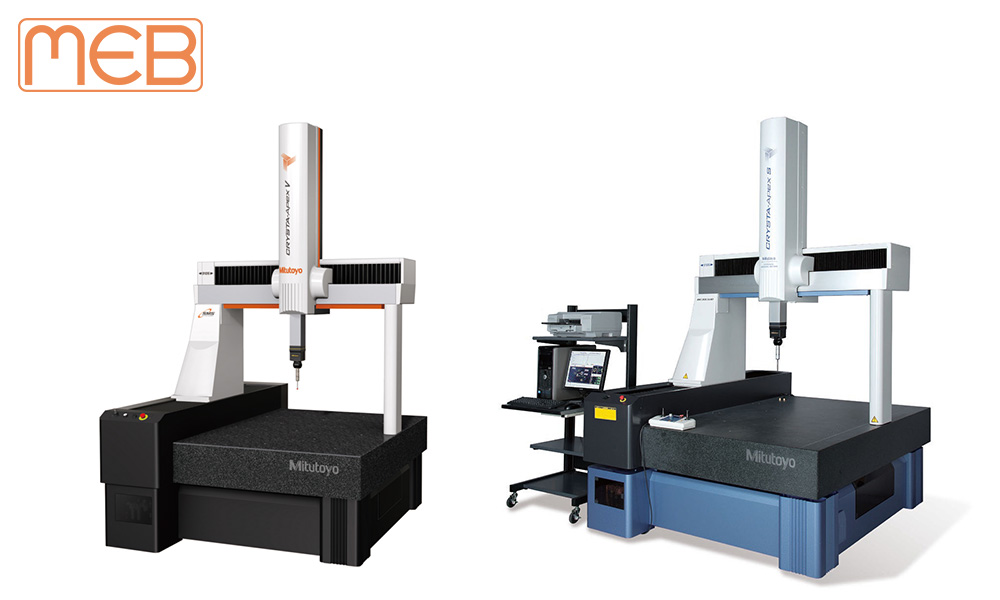
Coordinate Measuring Machines (CMM): Precision in Measurement
A Coordinate Measuring Machine (CMM) is a highly accurate device used to measure the geometric attributes of three-dimensional objects. By utilizing a probe to sense discrete points on an object's surface, CMMs can determine its dimensions, shape, and other geometric characteristics with exceptional precision.
Key Features and Benefits of CMMs:
- High Accuracy: CMMs are renowned for their ability to measure with micron-level precision, ensuring the accuracy of manufacturing processes and quality control.
- Versatility: CMMs are capable of measuring a wide range of objects, from small components to large assemblies, making them indispensable in various industries.
- Efficiency: CMMs can automate the measurement process, reducing human error and increasing productivity.
- Data Analysis: CMMs can collect and analyze measurement data, providing valuable insights into product quality and process control.
Types of CMMs:
- Contact CMMs: These machines use a mechanical probe to measure the surface of an object.
- Non-Contact CMMs: These machines utilize technologies like lasers or optical sensors to measure objects without physical contact.
Applications of CMMs:
- Manufacturing: Quality control, reverse engineering, and dimensional inspection.
- Aerospace: Inspection of complex components, such as turbine blades and aircraft parts.
- Automotive: Quality assurance of car parts, including engines, transmissions, and body panels.
- Medical Devices: Verification of implant dimensions and tolerances.
- Research and Development: Prototyping and testing of new products.
In conclusion, Coordinate Measuring Machines are essential tools for ensuring precision and quality in manufacturing and other industries. Their ability to accurately measure complex geometries makes them indispensable for a wide range of applications.